Top: Food waste is a nitrogenous feedstock that generators typically will pay a fee to have processed. Photo by Nora Goldstein
Craig Coker
Planning a new merchant organics recycling facility requires considerable thought and investigation. As the old adage goes, “Proper prior planning prevents poor performance.” While organics recycling facilities have a certain “Field of Dreams” cachet about them, i.e., “If you build it, they will come,” serious investors will want to see a well thought out business plan. A facility plan is the cornerstone of the business plan for a merchant organics recycling facility.
One of the first steps in the facility planning process is to define, as best as possible, a waste capture plan for the proposed facility — essentially an assessment of potential waste materials where their generators are willing to pay a processing fee within a certain geographic area. The waste capture plan also addresses those compostable materials in that geography that are capturable, but for which processing fees are unlikely (e.g., animal manures), or, for materials that an organics recycler would have to pay for (e.g. kiln-dried sawdust, poultry litter). At this early stage in the process, consider everything. The less favorable feedstocks will fall out in the financial analysis later in the planning process.
How big a geographic area would you search? That depends in large part on the quality of the transportation network in the area you plan to locate in. One rule-of-thumb is that a one-hour travel time (one-way) between either compostable waste sources and/or compost product outlets, and the organics recycling facility, is the upper end of financial feasibility for hauling. This makes sense, if you consider that hauling a 24-ton tractor-trailer load 50 miles adds about $9.38/ton to the cost of transport (this assumes a haul cost of $4.50/loaded mile, which may be low, given the recent run-up in diesel fuel prices). So, if your preferred site is in a rural area of two-lane roads, your geographic search radius is about 50 miles; if your site is within five miles of an interstate highway, that radius might increase to 75 to 100 miles. This is not a hard-and-fast rule; I know of several composters receiving industrial food processing residuals from plants 175 to 200 miles distant from the composting facility.
Nitrogenous Materials Search
The search should begin with nitrogenous (nitrogen-rich) wastes, as these are the most likely to be materials that generators are accustomed to having to pay a processing fee:
Unstabilized Sewage Sludges
Sewage sludge is composed of both inorganic and organic materials, large concentrations of some plant nutrients, much smaller concentrations of numerous trace elements and organic chemicals, and some pathogens. The composition of sewage sludges vary considerably depending on the wastewater composition and the treatment processes used. Note that the term “biosolids” refers to sewage sludges that have undergone sufficient treatment for stabilization and pathogen reduction (such as composting), and that are of sufficiently high quality to be land applied. In this case, the search would focus on raw (unstabilized) sewage sludges.
Some merchant composting facilities accept sewage sludges as feedstocks, however, merchant anaerobic digestion (AD) facilities for sewage sludges are rarer, insofar as there are over 1,200 wastewater treatment facilities in the U.S. that have their own AD facilities for sewage sludges. While sewage sludges can command high processing fees, they are the most heavily regulated composting feedstock, which will drive up front-end facility capital costs. Also, sewage sludges are produced 24/7/365, so merchant facilities have to have both adequate capacity and a solid contingency plan in the event of facility problems. As having adequate sludge management capability is critical to the wastewater treatment plant’s performance and permit compliance, most wastewater authorities are reluctant to deal with any but the most-seasoned and experienced merchant composters.
All wastewater treatment plants are required to file annual reports on how much sewage sludge is produced and how they are managed. These can usually be obtained by filing a Freedom of Information Act (FOIA) request with the State environmental regulatory agency. Most sewage sludges are recycled or disposed under multi-year contracts issued by the treatment plant or sanitation authority and you may have to wait until the contract is publicly rebid.
Industrial Process Sludges
These sludges are produced by the pretreatment of industrial wastewaters created by the manufacturing processes used. They may or may not include sanitary wastes, which can influence both acceptance feasibility and facility permitting. Process sludges most suitable for recycling via composting or AD are those arising from industrial food processing facilities. Non-food industrial process sludges may be acceptable feedstocks depending on sludge quality. One composter in Virginia accepts a process sludge from a facility that manufactures cellulose acetate from wood chips. These sludges are often the high-moisture content (85%+) residual from dissolved air flotation (DAF), which can be a handling challenge at composting facilities.
Estimating quantities of capturable process sludges can be a challenge as this information is often viewed as proprietary. One place to start is with business directories, either browsing Chamber of Commerce membership listings, or by purchasing a list of industries in particular North American Industrial Classification System (NAICS) codes or from a service like Data Axle. These lists can be purchased for particular geographies. NAICS codes are 6-digit codes; those beginning with 31, 32 or 33 cover manufacturing. Once you have identified a particular industry in your geographic search area, the next step is to contact the wastewater treatment staff to find out more about their wastes and what they do with them. One approach is to talk to salespeople in the wastewater polymers industry (polymers are used to enhance sludge dewatering), as they often know of industries looking for recycling alternatives for process sludges.
Like sewage sludges, these process sludges are often recycled via land application under multi-year contracts. While land application of process sludges is often much cheaper than the processing fee at a composting or AD facility, the need for good weather to apply them, plus nutrient management limitations in water-quality impaired watersheds (along with land development), can make the more reliable outlet of composting or AD more attractive to an industry, even if the cost is higher. Industrial environmental professionals managing a plant’s wastes will almost always insist on a site visit to verify that your organics recycling facility is properly operated and free of any regulatory complications. In fact, it is a good practice with industrial feedstocks to engage in mutual site visits, so each can understand how the others’ manufacturing processes work.
Industrial Food Processing Residuals
Included in this category are process line start-up and shut-down wastes, spillages, packaging errors, out-of-date foods, and recalled foods. Often, these feedstocks will need to be depackaged prior to recycling. One composter in Virginia had a contract to receive various sized bags of dry dog food; the food was depackaged by hand and incorporated into windrows. The empty bags were taken to the nearby sanitary landfill and photographed as the landfill operator covered the bags with trash. The photos were then sent to the manufacturer of the dog food to certify the destruction. Identifying sources and estimating quantities of these wastes is done the same way as for industrial process sludges.
ICI Food Wastes
For sourcing and estimating quantities of industrial, commercial and institutional (ICI) food wastes, I use the U.S. EPA’s Excess Food Opportunities Map for an initial approximation of potentially capturable quantities. The map can be adjusted to cover different geographies and provides both a low and a high estimate of potential food waste generation. The generation factors for each category (correctional and educational facilities, hospitality, healthcare, food processors and manufacturers, wholesale and retail food sources and restaurants and food services) are based on industry studies in each sector (EPA, 2020). The ranges between the low estimates and the high estimates can be quite large, reflecting underlying differences in how the original generation studies were performed.
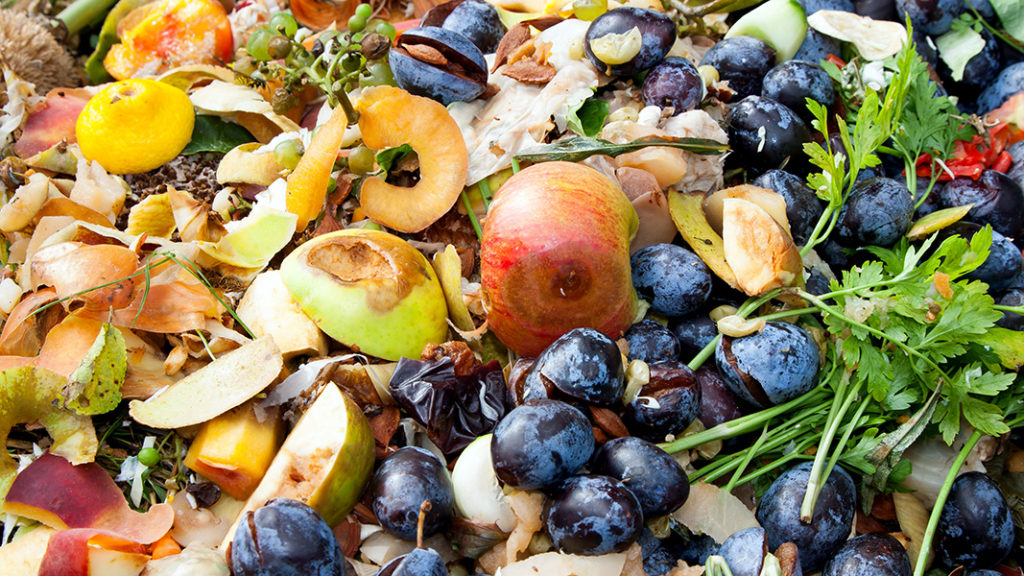
The U.S. EPA’s Excess Food Opportunities Map can be used for an initial approximation of potentially capturable quantities of ICI food waste.
The map also provides contact information for each source in each category for individual follow-up. If your new facility is going to locate in a state or community that already has implemented a food waste diversion program affecting ICI generation sources, detailed projections may be available from the local recycling coordinator.
Residential Food Wastes
Residential food waste generation estimates can be compiled from research the NRDC (Natural Resources Defense Council) did in Nashville (TN), New York City and Denver. It estimated food waste generation to be 3.5 pounds (lbs)/person/week or 8.7 lbs/household/week (NRDC, 2017). Updated 2020 population data by state, county or by census tract is available from the U.S. Census. Similar to ICI wastes, detailed projections may be available from the local recycling coordinator if your new facility is locating in a state or community with an existing residential food waste diversion program.
For new voluntary or subscription food waste collection programs, you should adjust your generation estimates for realistic estimates of participation rates and setout rates. Participation rates are the percentage of households who will sign up for the program. This will increase gradually over time, likely from 15% to 20% by the end of year one to ≈ 45% to 55% by the end of year five. Setout rates are the percentage of signed-up households who actually have something to collect on each collection day, which can be influenced by vacation schedules and winter weather. In northern climates, setout rates might be as low as 25% in winter. Setout rates following national holidays will likely be very high.
Animal Manures
Livestock farmers rarely will pay a processing fee for recycling their herds’ manures, and, in the case of poultry litter, can command a purchase price of $25 to $30/ton FOB (freight on board) at the poultry farm. In the case of horse manure, there is usually so much bedding mixed in with the manure that it actually has a carbon-to-nitrogen ratio of more than 30:1. Manures vary widely in terms of moisture content, with swine and dairy manure having the highest and poultry litter the lowest. High moisture manures are very suitable for AD. Several poultry litter AD plants have come online in recent years.
Estimating herd and flock counts is available from the U.S. Dept. of Agriculture’s National Agricultural Statistics Survey, which is done every five years (the update is scheduled for later in 2022). Herd counts are available by state and county for virtually all forms of livestock, although specific numbers are not reported when there are only a few farms raising particular herds or flocks. The 2017 Survey results can be queried at this website and local Cooperative Extension personnel will likely have interim updated numbers. Manure quantities per head of livestock can be found in references such as the Livestock Waste Facilities Handbook ((MWPS, 1985).
Animal Mortalities
Animal mortalities are very rarely transported off-farm for recycling at merchant composting facilities (they are not suitable for AD) due to animal health and disease transmission concerns. If you are planning an on-farm composting operation, you may find opportunities to help animal agriculture farms with routine mortalities (estimated at about 5% of herd or flock size annually), and you may have opportunities to develop separate composting operations on a farm for catastrophic mortality losses. It is unlikely you will receive any processing fee for routine mortalities, but, in many states, there may be disaster relief funds available for catastrophic mortality composting.
Agricultural Wastes
The vast majority of agricultural wastes are very compostable, but farmers often leave them in the field as they are expensive to collect and transport, and they provide protection against erosion in between crop cycles. One notable exception is cotton gin trash (CGT) — the residual from the first cleaning of cotton from harvested plants. CGT is relatively high in nitrogen; one composter in South Carolina uses CGT to help balance C:N ratios for land-clearing debris they compost. Like animal manures, processing fees are unlikely for agricultural wastes.
Carbonaceous Wastes
Waste capture plans should also address carbonaceous (carbon-rich) wastes, which are needed to keep compost pile C:N ratios near the desired 25:1 to 30:1 level. These types of wastes include:
Yard Wastes
Seventeen states ban leaves, grass clippings and/or brush (a.k.a. yard wastes) from landfilling. Another four states ban it unless the landfill has a gas collection system (USCC, 2021). If your planned facility is in one of those states, the environmental regulatory department likely has good data on yard waste generation in various counties and cities. Many municipalities in yard waste ban states will have residential curbside collection programs set up. Some run their own mulching and composting facilities while others look to the private sector to handle those materials (usually under contract to the municipality).
In other states, you could use EPA’s estimate of 12.11% of the municipal solid waste (MSW) stream being comprised of yard wastes (EPA, 2022). All states track annual generation of MSW. I have used a preliminary generation rate of 0.1 tons/person/year based on tonnages monitored by several municipalities in the mid-Atlantic states.
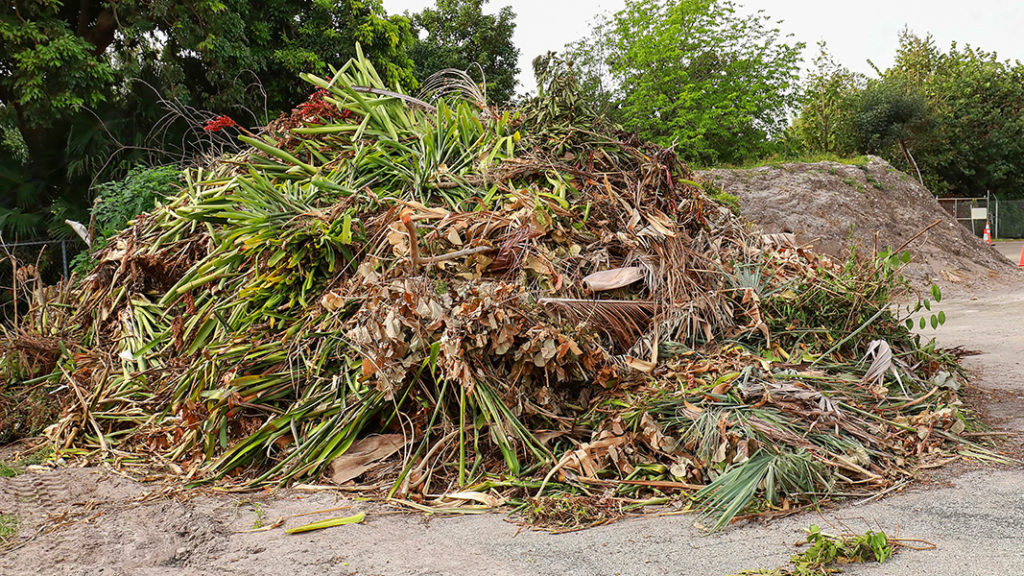
In states with yard waste disposal bans, data may be available on the quantities generated in specific localities.
It may be possible to get processing fees for yard wastes (some composters will accept them for free just for the carbon). This is most likely if your facility is contracted by a municipality to process its yard wastes. For a purely merchant transaction with commercial landscapers, the processing fee can be based on volume or on weight, if your facility will have scales. If you are not planning on having scales, your volumetric processing fee should be based on size of vehicle delivering the yard waste, not on visual estimates of volume in a vehicle.
Other Carbonaceous Feedstocks
- Land-Clearing Debris: This is a more difficult waste stream to quantify as tonnages or volumes are rarely tracked. In addition, the variations in vegetation on undeveloped sites make it difficult to develop a generation factor such as: “X acres of clearing = Y cubic yards of wood chips.” One approach is to try to interview some excavation/clearing contractors in your community to find out what they do with their land-clearing debris now. Keep in mind that this waste stream may require specialty equipment to process, such as shearing attachments for excavators to split open tree trunk stumps. The processing fee considerations noted above for yard wastes also apply to this waste stream.
- Sawdusts/Shavings: This is another waste stream that is difficult to quantify as the amount produced by sawmills, furniture plants, etc. varies widely depending on tree species, tree sizes, saw blade thickness, etc. This is also a feedstock composters often have to pay for; a Virginia composter is currently paying $50/ton ($8.75- $12.50/CY) for kiln-dried hardwood sawdust with a C:N ratio of 308:1.
- Forestry Wastes: Slash is the term used to describe the treetops, limbs and other woody material left behind after a timber harvest. The amount of slash left behind will depend on several factors, including the size and quality of the harvested trees. While this can be a good source of carbon, the cost of collecting, grinding and transporting it may be excessive. Opening dialogues with tree harvesters who precede land-clearing contractors on construction sites may yield some opportunities to capture these wastes. It is unlikely any processing fees can be charged.
- Construction Wastes: Several programs have been attempted over the years to segregate clean wood waste from construction sites for recycling. As most wood-based construction materials are engineered wood products (e.g. plywood, oriented strand board, medium-density fiberboard, etc.), these products have been deemed unsuitable for composting by most state regulators. Several pilot tests I’ve conducted since the 1990s have proven that the concerns about residual urea-formaldehyde (UF) glues in the final compost are unfounded. Composters interested in this waste stream should conduct their own pilot tests to prove to regulators that composting will degrade the UF glues. These wastes are often landfilled, but if they are source separated properly for composting, a competitive processing fee should be obtainable.
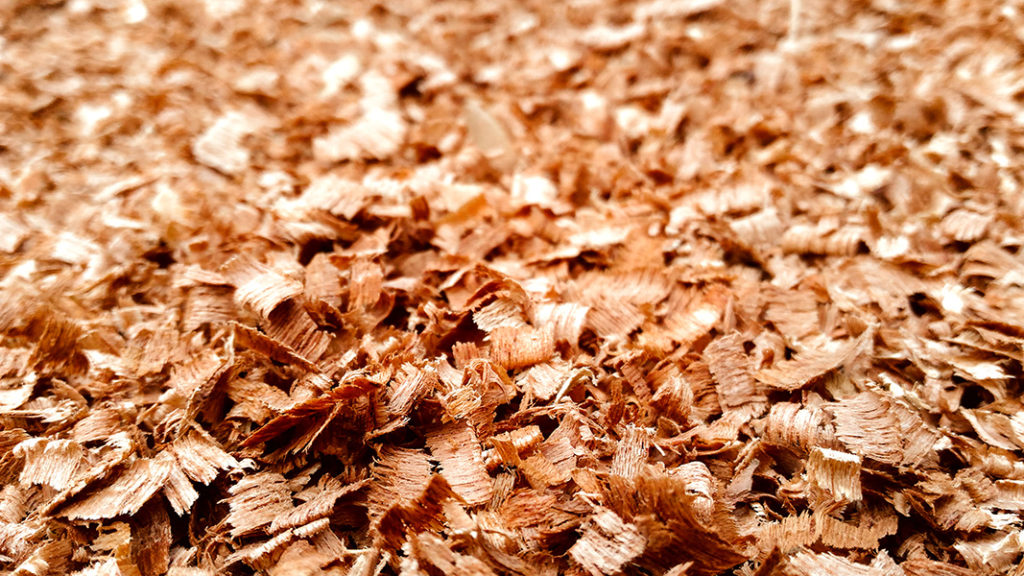
The amount of sawdust or shavings (above) produced by sawmills, furniture plants, etc. varies widely depending on tree species, tree sizes, saw blade thickness, etc.
Processing Fees
Processing fees should be based on your projected cost of production (on a per ton or per cubic yard) basis but be sensitive to competition. In most cases, your primary competition will be the local landfill, and while their tipping fee rates may be tailored to particular generators, pricing compost processing fees at 80% to 90% of the stated gate rate for MSW tip fees should provide the economic “magnet” to pull wastes towards your organics recycling facility.
A well thought out waste capture plan can provide one of the answers to “How big should my new organics processing facility be?” The other question to be answered is “How much compost/soils/digestate will my market absorb?” That is a topic for another article in this series.
Craig Coker is CEO of Coker Composting & Consulting near Roanoke VA and is a Senior Editor at BioCycle CONNECT. He can be reached at ccoker@cokercompost.com.